What are the difficulties in the civil construction of water parks?
The civil construction of water parks faces numerous technical and management challenges due to their specialized functional requirements and the complexity of water-related engineering. Below is a detailed analysis of key difficulties and mitigation strategies:
I. Complex Foundation Treatment
- Unpredictable Geological Conditions
- Challenge: Large-scale pool excavations (e.g., wave pools, lazy rivers) may encounter soft soil, karst caves, or underground rock layers (as seen in blasting cases), leading to insufficient bearing capacity or leakage risks if geological surveys are inadequate.
- Mitigation: Conduct high-precision ground-penetrating radar surveys; reinforce weak foundations with soil replacement, pile foundations, or grouting; pre-plan blasting or mechanical crushing for rocky strata.
- Groundwater Control
- Challenge: High groundwater levels during pool excavation can cause collapses or seepage, jeopardizing safety.
- Mitigation: Implement well-point dewatering, curtain waterproofing (e.g., steel sheet piles, jet grouting), or open drainage with pumping to ensure dry working conditions.
II. Waterproofing and Anti-Leakage Engineering
- Large-Scale Pool Impermeability
- Challenge: Pools (especially irregularly shaped structures) must withstand long-term water pressure, with joints and corners prone to cracking and leakage. Traditional concrete self-waterproofing often falls short.
- Mitigation:
- Materials: Use P8-grade or higher impermeable concrete combined with flexible waterproof layers (e.g., SBS membranes, polyurethane coatings).
- Techniques: Optimize construction joint placement; install water-expanding sealing strips; use post-pouring strips to minimize shrinkage cracks.
- Pipe Penetration at Pool Walls
- Challenge: Pipe penetrations (for water supply, drainage, and circulation systems) create vulnerable leakage points.
- Mitigation: Pre-embed rigid waterproof sleeves; seal secondary gaps with micro-expansion concrete and waterproof sealants.
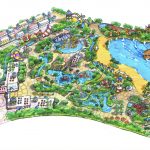
III. Mass Concrete Construction
- Thermal Stress Control
- Challenge: Thick pool foundations generate significant hydration heat, risking temperature differential cracks.
- Mitigation:
- Materials: Use low-heat cement blended with fly ash or slag to reduce heat generation.
- Construction: Pour concrete in layers; embed cooling pipes; cover with insulation to limit temperature differentials to ≤25°C.
- Anti-Float Design
- Challenge: High groundwater levels can cause empty pools to float, damaging structures.
- Mitigation: Increase dead load (e.g., thicker base slabs); install anti-floating anchor rods or permanent dewatering wells.
IV. Irregular Structures and Embedded Component Precision
- Slide Support Foundation Alignment
- Challenge: High-speed slides require foundation flatness and embedded part positioning accuracy ≤3mm; deviations hinder equipment installation.
- Mitigation: Use total stations for real-time positioning; weld embedded parts to reinforcement; conduct post-pouring alignment checks.
- Integration with Thematic Structures
- Challenge: Decorative elements (e.g., artificial rock walls, sculptures) require synchronized pre-embedding of connectors to avoid damaging waterproofing during retrofitting.
- Mitigation: Use BIM for collaborative design; pre-reserve steel anchor points and utility channels.
V. Seasonal Construction Constraints
- Cold Weather and Rainy Seasons
- Challenge: Winter concrete pouring in northern regions requires freeze protection; rainy seasons in southern areas increase excavation collapse risks.
- Mitigation:
- Winter: Add antifreeze agents; erect heated enclosures; use steam curing.
- Rainy Season: Phase construction; install drainage ditches around excavations; prepare backup pumping equipment.
Case Studies and Lessons Learned
- Case 1: A wave pool lacking anti-float design heaved and cracked after groundwater rose during heavy rain, incurring over RMB 5 million in rework costs.
- Case 2: A 5cm deviation in slide foundation embedded parts led to equipment installation refusal by the supplier, causing a 2-month delay for rebar reinforcement corrections.
Key Management Measures
- Technical:
- Use BIM for clash detection to optimize interfaces between civil, MEP, and decorative works.
- Implement a “layer-by-layer inspection + water-tightness testing” regime for waterproofing (prohibit concealment until each stage passes inspection).
- Managerial:
- Involve equipment suppliers early in technical briefings to ensure embedded part accuracy.
- Establish emergency plans (e.g., rapid leak-sealing teams).
Water park civil construction must prioritize “waterproofing as the core, precision as the key” through meticulous design and full-process control to mitigate risks and ensure quality and schedule compliance.