Analysis of factors affecting the progress of water park projects
The factors influencing the progress of a water park construction project are multifaceted, encompassing both common challenges in general engineering projects and unique technical and management complexities specific to water parks. Below is a categorized analysis of the key factors:
I. Design and Pre-Construction Phase
- Delays in Design and Approval
- Water parks require a balance between functional engineering (e.g., slides, wave pools, lazy rivers) and thematic creativity. High design complexity often leads to repeated revisions and coordination delays.
- Specialized Requirements: Water circulation systems, waterproof engineering, and safety redundancies (e.g., anti-slip measures, emergency evacuation routes) must comply with strict regulations, potentially prolonging approval processes due to local safety or environmental standards.
- Unexpected Geological and Site Conditions
- Foundation treatments (e.g., anti-leakage measures for pools, insufficient load-bearing capacity) or underground utility relocations may require adjustments to construction plans if initial surveys are inadequate, extending timelines.
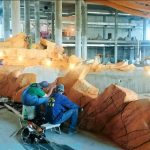
II. Critical Factors During Construction
- Complex Technical Challenges
- Hydraulic Engineering: Large-scale pool construction, fiberglass slide installations, and integrated water treatment systems (filtration, disinfection, temperature control) demand specialized teams. Technical errors can lead to rework.
- Thematic Packaging: Customized decorations (e.g., artificial rock formations, sculptures) may face delays due to intricate craftsmanship or supplier delivery issues.
- Supply Chain and Resource Management
- Dependence on Imported Equipment: High-end attractions (e.g., high-speed slides, wave generators) reliant on imports are vulnerable to international logistics delays or customs clearance bottlenecks.
- Seasonal Material Shortages: Fluctuations in the availability of waterproof coatings, specialty concrete, or other materials can halt construction.
III. External Environmental and Policy Constraints
- Climate and Natural Conditions
- Outdoor construction is susceptible to rainstorms, typhoons, or extreme heat (e.g., extended concrete curing periods). In northern regions, winter freezes may force work stoppages.
- Environmental and Safety Regulations
- Failure to obtain water usage permits or meet wastewater discharge standards (e.g., chlorine level controls) may require remake (work stoppages for rectification). Noise and dust complaints from nearby residents could restrict construction hours.
IV. Organizational and Coordination Risks
- Inefficient Multi-Party Collaboration
- Poor communication among designers, contractors, equipment suppliers, and supervision units can lead to workflow mismatches (e.g., equipment arriving before civil works are completed, occupying site space).
- Funding Instability
- Staggered or delayed funding may postpone critical equipment purchases or trigger subcontractor strikes.
V. Operational Preparation and Handover
- Commissioning and Trial Run Issues
- Leaks in water circulation systems or equipment compatibility failures (e.g., mismatched pumps and control systems) may require repeated debugging, consuming critical path time.
- Safety certification failures (e.g., slide impact force tests, lifeguard staffing) can delay opening schedules.
- Unforeseen Events
- Force majeure events like pandemics, labor strikes, or community protests may cause full project halts.
Water Park-Specific Case Studies
- Case 1: A project faced a 3-month delay due to insufficient production capacity at a fiberglass slide supplier, pushing back subsequent water treatment system installations.
- Case 2: Unforeseen underground bedrock during pool excavation required additional blasting, increasing costs and timelines by 20%.
Mitigation Strategies
- Pre-Construction: Conduct thorough geological surveys; adopt flexible designs; engage EPC contractors with water park expertise.
- Construction Phase: Maintain backup supplier lists; include penalty clauses for critical equipment delays; optimize workflows using BIM technology.
- Post-Construction: Align with regulators on handover criteria early; reserve a 1-2 month buffer for commissioning issues.
Proactive risk management can significantly reduce delays and ensure timely project completion and operation.